For your information
You are being redirected to one of our divisional subsites which contains more detailed information on the required division. To navigate back to the main Invicta Group site, please click the link found in the footer at the bottom of the page.
- Durasteel
Discover the benefits of Durasteel
- Systems
Systems
- Expertise
Expertise
-
Applications
- Aircraft Hangar Fire Protection
- Battery Storage Facilities
- Building Fire Compartmentation
- Anti-Terrorist Blast Protection
- Cable Tunnel Fire Compartmentation
- Equipment Delivery Hatches
- Equipment Enclosures
- Heat Shields
- Power Station Fire Protection
- Metro and Rail Fire Protection
- High Voltage Cable Protection
- Substation Fire & Blast Protection
- Tunnel Fire Protection
- Oil & Gas Fire & Blast Protection
- Ventilation Systems
- Wind Farm Fire Protection
-
Applications
- Projects
- Insights
Insights
-
Articles
- Blast Protection System Design Considerations & Design Criteria
- How to Conduct a Fire Risk Assessment for Factories and Warehouses
- Minimising the Risk of Fire, Blasts & Explosions in the Middle East
- Integrity, Stability and Insulation in Passive Fire Protection
- Triangle of Fire & Active vs Passive Fire Protection
- Frequently Asked Questions
- A to Z of Terms
-
Articles
- Contact
Contact
UK +44 1843 220 256
US +1 305 328 9444
UAE +971 4 277 6225
Qatar +974 4441 4340
India +91 79945 14049
Malaysia +60 16 286 6225
- Start your project
What Boeing’s downfall says about safety culture
20th August 2024
Quick Quote
Contact Benn Larkin Sarun Vysakham Ben Tan Anand Raghavan Anand Raghavan Our USA Office
To get a quotation or arrange a free site survey - Call Benn Larkin Sarun Vysakham Ben Tan Anand Raghavan Anand Raghavan Our USA Office on
-
UK
-
UAE
-
Malaysia
-
India
-
Qatar
-
USA
Current location:
Quick Quote
Contact Benn Larkin Sarun Vysakham Ben Tan Anand Raghavan Anand Raghavan Our USA Office
-
UK
-
UAE
-
Malaysia
-
India
-
Qatar
-
USA
Current location:
Until the turn of the 20th century, Boeing was one of the world’s most respected companies. Almost a century of manufacturing and engineering prowess had put it firmly at the top of the aircraft industry, outliving half a dozen major competitors. The events in recent months then may seem like a heady fall from grace, with passengers actively avoiding their aircraft.
Ask industry insiders, however, and this series of accidents and incidents has been a long time coming. Boeing’s downfall has been the story of a controversial corporate merger, and losing sight of the strict safety culture which brought it so much success. It’s a lesson which is relevant to safety in all industries – and one with tragic parallels in fire safety.
A fall from grace
The point at which the general public became aware of issues inside Boeing was the two crashes of the 737 MAX. These incidents in 2018 and 2019 hinged on faults in a system called MCAS, or the Maneuvering Characteristics Augmentation System. This system was designed to make the plane easier to fly for pilots who had been used to the previous 737 model. This was important because Boeing didn’t want pilots to have to do ‘type training’ for the new aircraft, as this would be a major expense for airlines.
MCAS was needed because the new plane used bigger and more powerful engines, which had to be positioned higher up and further back on the plane. This naturally changed the plane’s handling characteristics, and would certainly have required type training. The first problem was that Boeing simply didn’t tell pilots or regulators that it had instituted MCAS, or what the system did. The only mention of it anywhere was a vague reference to it in the plane’s manual.
The crashes resulted from an oversight in MCAS, where it only relied on a single sensor for critical flight data. This sensor – which can sometimes be accidentally covered or obscured by things like nesting insects – malfunctioned, causing MCAS to think that the plane was stalling. MCAS then pushed the plane’s nose down – an action which could not be overridden by the confused pilots, and which sent both planes into the ground.
Taking safety seriously
This combination of a software failure and the deliberate obfuscation of safety information should have caused earthquakes at Boeing. It was clear here that safety processes and controls hadn’t just failed on multiple levels. This kind of decision-making speaks to a kind of corporate culture that seems to trivialise safety, in an industry where safety is more consequential and more thoroughly legislated than almost any other.
Take an example that’s particularly relevant to us: fire safety. A fire onboard an aircraft is widely considered the most dangerous threat it can face. A fire that takes hold in the cargo hold – which may often store flammable materials, such as batteries – can quickly fill the cabin above with smoke, and eventually burn through the floor. It also risks burning through critical control cables, much as a building fire can compromise life safety systems. An in-flight fire is a major emergency, and can down a plane in as little as 15 minutes.
For evidence of this, consider the tragic case of Swissair Flight 111, which crashed over Canada on its way to New York. Poor maintenance of cables for the in-flight entertainment system – which had been rushed into service – likely caused a short which led to a devastating in-flight fire. On ValuJet Flight 592, meanwhile, improperly stored and labelled oxygen generators fed a fire that rapidly took down the aircraft. In both cases, thorough investigations led to sweeping reforms in aircraft construction, maintenance, and cargo procedures.
This is the usual response to accidents, a commitment to safety that has made air travel the safest form of public transportation. Any incident which poses a threat to life – even if it doesn’t lead to any fatalities or even injuries – must be reported and investigated. This relies on the willingness of pilots to report near-misses, which they are empowered to do as part of a no-blame culture. While further training may be required, genuine mistakes or oversights do not put pilots’ jobs at risk.
Safety on the backburner
You would think this would be Boeing’s approach after the MAX crashes. Indeed, the CEO who Boeing brought in after the disasters – Dave Calhoun – promised that the company had learned its lesson, and would overhaul its safety culture. A Safety Management System was drafted the year of the second crash, and implemented in 2020. Much was made at that time of the company’s efforts to make employees feel comfortable supporting safety breaches.
On paper, these improvements seemed substantial. The company’s own Caso report from 2023 highlights changes such as safety workshops, a new digital learning platform, and the success of its Speak Up! reporting system. Yet this artifice came crashing down when Alaska Flight 1282 (another 737 MAX) lost a door plug (designed to cover an unused door frame) mid-flight earlier this year. It was only by sheer luck that nobody was injured or killed, as the seats surrounding the door plug were empty on the flight.
An immediate investigation by the National Transportation Safety Board (NTSB) found that a number of the bolts designed to keep the door plug in place were never fitted, while the documentation of who worked on the plug was either missing or had never been recorded. Shortly afterwards, a Federal Aviation Administration (FAA) report into the previous 737 MAX crashes listed a catalogue of failures at Boeing, many of which it had still not adequately addressed, including a culture of fear among employees that they would be punished for revealing issues that slowed down production.
A messy merger
So how did a once-respected company characterised by great engineering reach this point? Many observers trace it back to 1997, when the company merged with competitor McDonnell Douglas. The CEO and many of the board members from the latter company came to control Boeing, and shifted its focus from engineering to bean-counting, with the CEO later outright stating that he wanted to run it more like a business than a great engineering firm.
A policy borrowed from General Motors led to the worst-performing 10% of managers being fired each year, causing widespread discontent. The company’s headquarters meanwhile were soon moved away from its manufacturing base in Seattle to Virginia, on the opposite side of the country. Many of its assets meanwhile were sold off, including facilities which manufactured its aircraft fuselages. The company formed to operate these facilities was Spirit AeroSystems – the manufacturer which fitted the faulty door plug on Alaska Flight 1282.
The potential impact of these changes ought to have been evident. McDonnell Douglas was struggling at the time of the merger, in large part thanks to a loss of trust in its aircraft. A series of deadly crashes plagued multiple different models, but most notably the MD-80, which suffered a notable issue with its cargo door. The door had been designed to open outwards to leave more room for cargo, but this required a complex locking mechanism to prevent it from being forced open from the difference in air pressure. Engineering oversights led this to fail in flight on two separate occasions, the second of which led to the deadliest ever single-aircraft accident without survivors.
Familiar lessons
It’s a tale as old as time, but it’s one that bears repeating. When we talk about fire safety, or racking safety in our sister division, it’s often in the context of adding additional safeguards. There’s a model that’s often applied to aircraft safety called the Swiss Cheese Model, where the more pieces of Swiss cheese you line up, the less likely it is that the holes line up. The metaphor is that the more safeguards and failsafes you put in place, the less likely a safety incident is to get past them, whether that means training, checklists, or passive fire protection.
What the model cannot survive is a lax safety culture. When the value of safety is diminished or made a secondary consideration, many of these barriers are bypassed. When production or manufacturing is rushed, mistakes happen. When jobs are outsourced to the lowest bidder, quality could be compromised. When employees are encouraged not to stop production for safety reasons, serious issues will go unreported. And all of this inevitably leads to unhappy employees, who make more mistakes, do lower quality work, and eventually leave, draining away talent.
Doing things safely doesn’t always mean doing them cheaply. But as with our Durasteel systems, the initial cost of a safety process, procedure, or system isn’t its ultimate cost. Inadequate or missing safety features can cost lives, and lead to severe penalties for businesses who skimp out. They can also – as in the case of Spirit AeroSystems – represent a short-sighted decision, which saves money in the short term, but costs more in the long run. This is something we often see with concrete fire and blast protection, where the cost of labour, curing time, and demolition to provide maintenance access can be much higher over time.
–
Our Operations Manager James Beale recently spoke about our steadfast focus on safety, and the importance of putting safety above all other considerations. Like the airline industry, safety is at the core of Invicta Durasteel as a company, and that extends from our products to the way they are installed on-site. Safety is non-negotiable, and the value of our products and services is rooted in both their quality and the trust this engenders.
The fundamental problem that has plagued Boeing is one that countless other companies continue to make: seeing safety as an obstacle, rather than an investment. Investment in safety and showing your commitment to safety reaps rewards all the way down the chain. Mistakes are caught, trust increases, long-term thinking is prioritised – and lives are ultimately saved. There can be few more important or consequential investments than that.
Accreditations & Affiliations

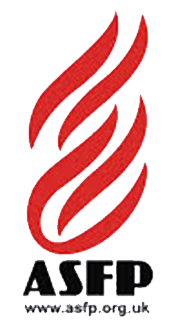
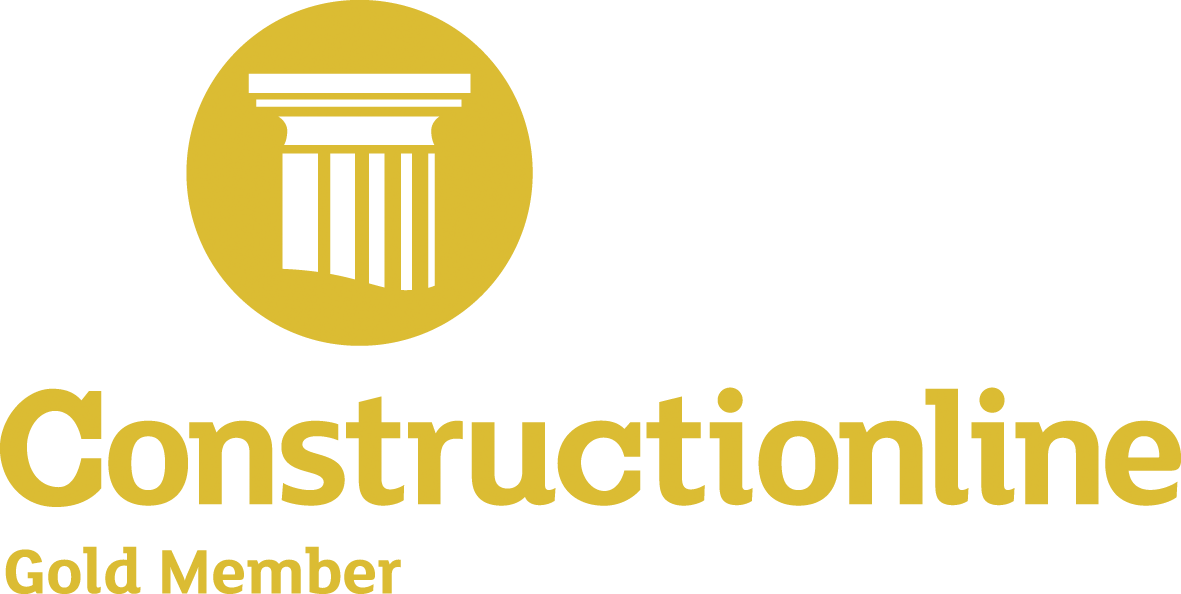
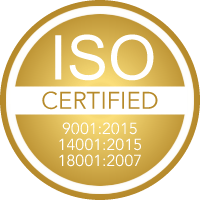
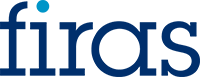
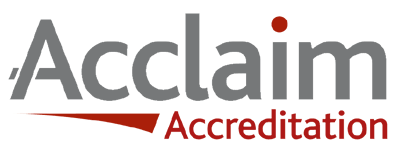
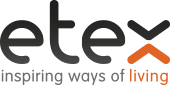
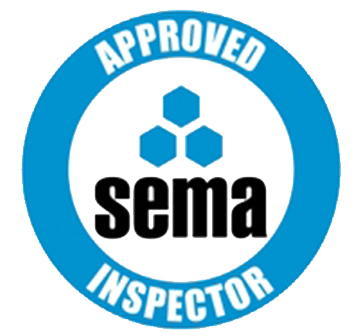
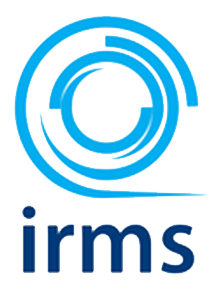
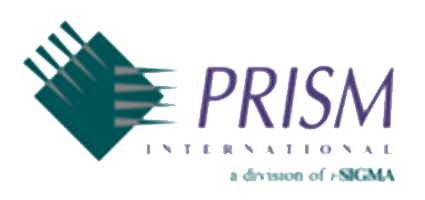
SpecUp - System Specification Wizard
Answer the 5 short questions below to receive your recommended Durasteel system specifications. Hover over the ? icons for a brief explanation.
Question 1/5
Type of system required?
Question 2/5
Fire rating required?
Question 3/5
Fire integrity-only or integrity and insulation?
Question 4/5
Fire attack risk from one side or both sides of the system?
Question 5/5
Blast rating required in addition to fire rating?
Creating your results page
Thanks for completing the SpecUp, you’ll be redirected to your results shortly.
Click here if you aren't redirected after a few secondsStart your project
Tell us about your project. Please complete this form. One of our sales team will come back to you with more details. If you prefer, you can drop us an email.
Share/Like this page