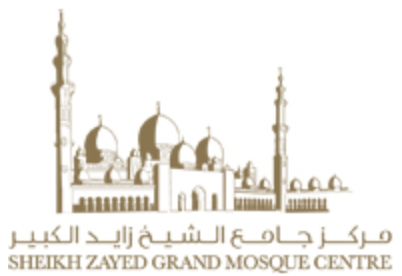
Application
Underground Smoke Extraction Ducts
Fire Rating
1 Hour
Project Duration
9 Months
Company profile
The Sheikh Zayed Grand Mosque is one of the largest mosques in the world, and a major site for both worshippers and tourists in Abu Dhabi. Named after Sheikh Zayed bin Sultan Al Nahyan, the Founder of the United Arab Emirates, the Sheikh Zayed Grand Mosque welcomes up to 55,000 visitors every day, and boasts both the largest hand-woven carpet in the world and one of the largest chandeliers in any mosque.
Operated by Sheikh Zayed Grand Mosque Center, the mosque was built as a centre of learning and a place of cultural exchange between Islam and the wider world. Its structures include an extensive library in the northeast minaret, the main prayer hall (hosting up to 7,000 worshippers), two smaller prayer halls (for men and women respectively), and an elaborate series of illuminated columns and pools.
Project challenge
Invicta was approached by project consultant Parsons Corporation to address issues with the design and operation of the existing GI duct ventilation and smoke extraction system in the basement parking area.
Due to its position below the water table, the existing underground GI duct ventilation system in the basement parking area had become filled with sea water, and had as a result become severely corroded. While a water pump extraction system had been retrospectively installed, this was not enough to mitigate the damage caused by the flooding, and the efficient operation and integrity of the system were being impeded.
As the main contractor on the project, Invicta was tasked with redesigning and improving the fire-rated ventilation and smoke extraction performance of the parking area underneath the mosque. In doing so, we would not only have to replace the existing GI duct system in a way that resolved the water table issue, but also improve its aesthetic appearance within the parking area, and limit disruption to the parking area during construction.
Technical constraints
Where the existing duct system utilised a series of trenches that ran below ground level and were embedded within the concrete slab, the new Durasteel fire-rated duct system would have to run above ground level, utilising the existing space between the building I-girders at ceiling level. This would encompass both fresh air supply and smoke extraction ducts, which would connect to the existing fan system in mechanical rooms located at the far end of the parking area – a process which would require the creation of new wall openings within the structural diaphragm wall to allow the ducts to pass through.
As well as removing and blanking off the existing duct system, the creation of a new above-ground ventilation system would also require extensive rerouting of other critical building services which clashed with the positioning of the proposed new duct system. This included the rerouting of fire sprinklers, cable trays, lights and other utilities.
Installed solution
Invicta designed, supplied, installed, tested and commissioned Durasteel 1-hour fire-rated supply and extract ducts between the structural I-girders, including connections to existing fans in the mechanical rooms. The extraction duct was designed with the addition of high-performance insulation board internally, providing thermal protection to the concrete structure in the event of hot smoke extraction during a fire. The duct system was designed to finish flush with the underside of the I-girders, and painted to match the existing surrounding structure, effectively rendering the duct system invisible to the naked eye.
Invicta also supplied and installed 96 fire-rated metal grilles to the supply and extract ducts, balanced in order to ensure even air distribution and smoke extraction throughout the parking area. 19 new wall openings between the mechanical rooms and car park were also constructed, while the existing GI duct openings were closed off, and 46 existing louver towers were removed.
All existing building services that clashed or conflicted with the proposed duct system were removed, capped and rerouted as required. Finally, Invicta supplied and installed 850m² of curved cladding around the areas where the Durasteel ducts passed under the inverted T-beams. This included 12 illuminated advertising boards that matched the aesthetics of the existing parking area and provided tangible benefits to visitors.
Key benefits
As the main contractor on the project, Invicta successfully designed, supplied and installed the new fire-rated ventilation system in the basement parking area within the given timeframe. As well as drastically improving the life safety of the area for the general public in the event of a fire, the removal and rerouting of old building services and louver towers and the installation of curved cladding and illuminated advertisement boards have significantly improved the aesthetics of the parking area.
Share/Like this page