For your information
You are being redirected to one of our divisional subsites which contains more detailed information on the required division. To navigate back to the main Invicta Group site, please click the link found in the footer at the bottom of the page.
- Durasteel
Discover the benefits of Durasteel
- Systems
Systems
- Expertise
Expertise
-
Applications
- Aircraft Hangar Fire Protection
- Battery Storage Facilities
- Building Fire Compartmentation
- Anti-Terrorist Blast Protection
- Cable Tunnel Fire Compartmentation
- Equipment Delivery Hatches
- Equipment Enclosures
- Heat Shields
- Power Station Fire Protection
- Metro and Rail Fire Protection
- High Voltage Cable Protection
- Substation Fire & Blast Protection
- Tunnel Fire Protection
- Oil & Gas Fire & Blast Protection
- Ventilation Systems
- Wind Farm Fire Protection
-
Applications
- Projects
- Insights
Insights
-
Articles
- Blast Protection System Design Considerations & Design Criteria
- How to Conduct a Fire Risk Assessment for Factories and Warehouses
- Minimising the Risk of Fire, Blasts & Explosions in the Middle East
- Integrity, Stability and Insulation in Passive Fire Protection
- Triangle of Fire & Active vs Passive Fire Protection
- Frequently Asked Questions
- A to Z of Terms
-
Articles
- Contact
Contact
UK +44 1843 220 256
US +1 305 328 9444
UAE +971 4 277 6225
Qatar +974 4441 4340
India +91 99 0355 9793
Malaysia +60 16 286 6225
- Start your project
How offshore fire safety has changed since Piper Alpha
13th February 2019
Quick Quote
Contact Fraser Shearer Sarun Vysakham Ben Tan Azim Rizvi Anand Raghavan Our USA Office
To get a quotation or arrange a free site survey - Call Fraser Shearer Sarun Vysakham Ben Tan Azim Rizvi Anand Raghavan Our USA Office on
-
UK
-
UAE
-
Malaysia
-
India
-
Qatar
-
USA
Current location:
Quick Quote
Contact Fraser Shearer Sarun Vysakham Ben Tan Azim Rizvi Anand Raghavan Our USA Office
-
UK
-
UAE
-
Malaysia
-
India
-
Qatar
-
USA
Current location:
How offshore fire safety has changed since Piper Alpha
Towards the end of last year, the oil and gas industry marked a solemn occasion: the 30 year anniversary of the Piper Alpha disaster. The deadly incident on a North Sea oil rig in 1988 shook the whole world, with the loss of 178 lives still standing as the most in any offshore oil disaster. A series of mistakes led to several explosions which destroyed critical infrastructure, and undermined efforts to escape and fight the flames.
The industry ought to have been roused to action by this tragic incident, and changes have certainly been made to ensure that it doesn’t happen again. Yet incidents such as Deepwater Horizon reflect both the persistent hazards on offshore oil rigs and the work that still needs to be done. The industry cannot afford to be complacent, and this anniversary already seems to be serving as a wake-up call.
A disaster in retrospect
As with so many disasters, a fatal series of errors caused a chain reaction of events that led to the immense loss of life on Piper Alpha. A critical maintenance procedure on an oil pump had been left unfinished, with the engineer leaving instructions for the control centre not to turn it on. Poor permit to work and handover protocols meant that the note was misplaced in the control centre, and the instruction was not passed on to the next shift.
When a blockage occurred in one of the pipes on the platform, the platform’s supervisors had to make a snap decision: turn on the inactive pump or lose power to the entire platform, shutting down production for several days. Having found no notes about the pipe, and without the time to inspect it manually, they decided to turn it on anyway. Missing a safety valve, condensate leaked and exploded, destroying the control centre and setting the platform ablaze.
Without the control centre, there was no infrastructure left to send an evacuation notice to the other workers, or to rally people to cut the lines feeding the fire with oil and gas from other platforms nearby. As a result, the fire raged and ruptured the platform’s gas lines while many workers retreated to their fire resistant quarters. Those quarters were eventually overwhelmed and destroyed, with only 68 people escaping the platform with their lives.
Immediate lessons
Although the enquiry took some time, its conclusions were stark, and revealed glaring issues in both the approach to augmenting oil rigs and the safety protocols which governed them. The most systemic issues arose from the conversion of the rig to mine both oil and gas. The need to add a gas module meant that the usual safety critical approach – keeping crewed areas far away from gas and oil modules – was abandoned.
Because the rig had been converted from pumping oil to oil and gas, it had also not been retrofitted with the explosion and impact resistant fire barriers normally required on gas-specific rigs. Both of these factors proved to be fatal when the initial explosion ruptured the nearby control centre and damaged the gas line, preventing any organised response to the disaster.
The problems with the maintenance system and lines of communication also came into stark relief. A shift change occurred without passing on the warning about the missing safety valve; the note about the valve left during the shift change was misplaced; and the pump was not manually checked before the decision was made, all clear and flagrant oversights. The pressure from above – taking these steps would have cost millions in lost revenue due to the time needed to stop and restart the rig – was also a massive contributing factor.
There were also decisions taken for safety which were of questionable value, and came to undermine efforts to fight the fire. Some of the firefighting equipment was destroyed in the initial blast, but fire water pumps which could have helped had been switched to manual operation, to protect divers who had recently been in the water from being sucked into the intakes. Yet there was little risk of this ever occurring, and the protocol on other rigs was to provide temporary overrides to this system, communicating closely with the divers instead. On Piper Alpha, the water fire pumps were almost permanently set to manual mode, prioritising diver safety over that of the rig.
Thirty years on
One of the most substantial conclusions from the 1990 report into the disaster was that safety management, rather than rules and regulations, was broadly to blame. Training, protocols and procedures were not alien concepts in 1988; they were simply ignored, or lapsed, or sparsely implemented. In some ways, it took a disaster like this to shake people into action, and demonstrate the consequences of ignoring rules that were sometimes interpreted as guidelines.
In this sense, significant improvements have been made. The establishment of Step Change In Safety in 1997 has seen the UK take a leading role in preventing any similar incidents in the oil and gas industry, making the UK a world leader in rig safety. The HSE took control of inspections and enforcement from the Department of Energy, and became more rigorous in both its checks on safety protocols and features, and the efforts of companies to incentivise and improve safety.
Yet these lessons haven’t permeated elsewhere – including facilities run by British companies. An incident at BP’s Texas City refinery in 2005 was followed by the same company’s infamous Deepwater Horizon disaster. In both cases, a culture which prioritised performance over safety was noted by investigators. The loss of life was significantly lower in the latter case, which can partly be put down to improvements in training and disaster management. But it reflects the reality of the industry: that danger is persistent, and that more can always be done.
—
As we get further and further away from the Piper Alpha disaster, the challenge will be in maintaining the shock value that story initially had. Without a new disaster – and we can only hope there is never anything equivalent again – newer generations may not feel the same impetus to implement safety protocols to protect against the minute risk of disaster. As Churchill once said, those who cannot remember the past are condemned to repeat it.
Accreditations & Affiliations

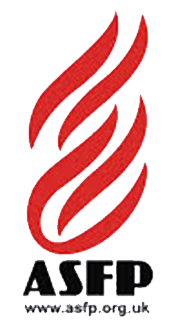
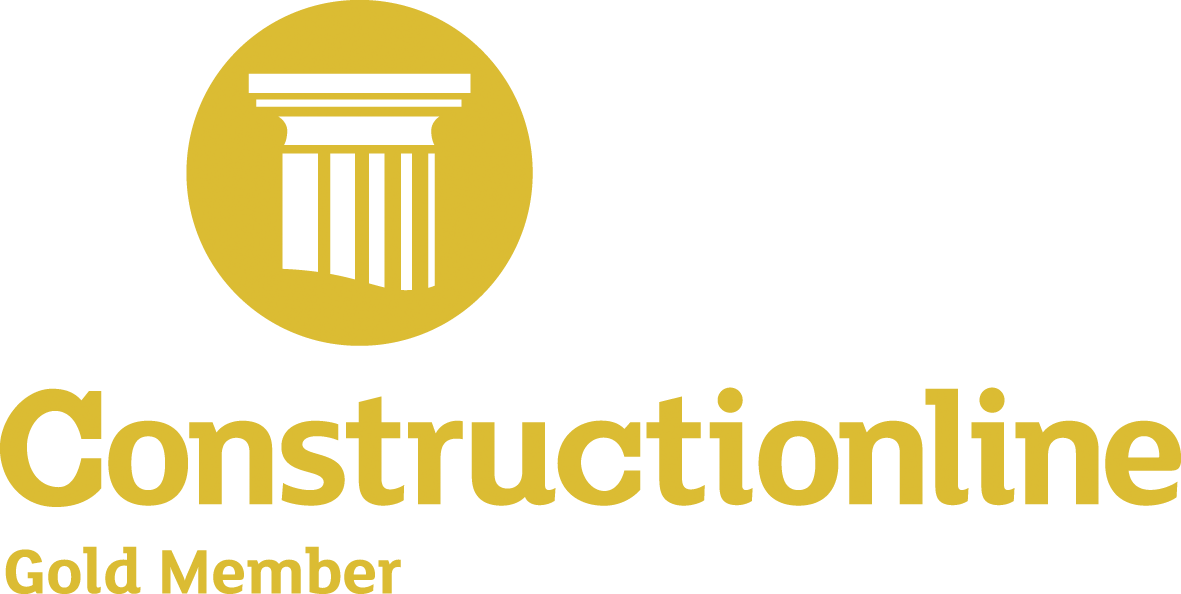
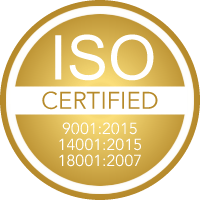
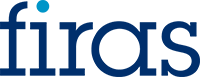
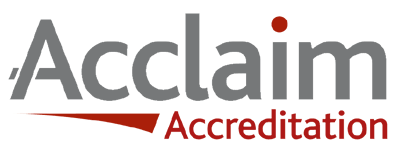
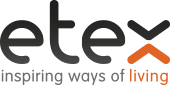
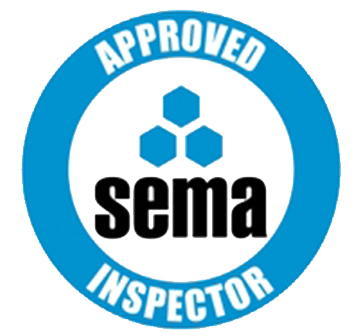
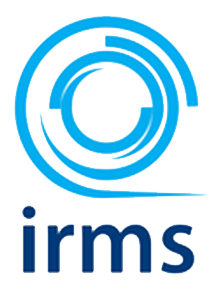
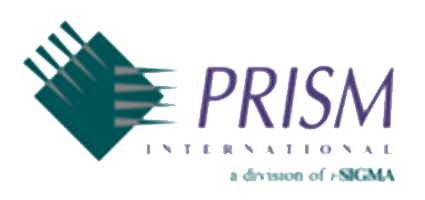
SpecUp - System Specification Wizard
Answer the 5 short questions below to receive your recommended Durasteel system specifications. Hover over the ? icons for a brief explanation.
Question 1/5
Type of system required?
Question 2/5
Fire rating required?
Question 3/5
Fire integrity-only or integrity and insulation?
Question 4/5
Fire attack risk from one side or both sides of the system?
Question 5/5
Blast rating required in addition to fire rating?
Creating your results page
Thanks for completing the SpecUp, you’ll be redirected to your results shortly.
Click here if you aren't redirected after a few secondsStart your project
Tell us about your project. Please complete this form. One of our sales team will come back to you with more details. If you prefer, you can drop us an email.
Share/Like this page